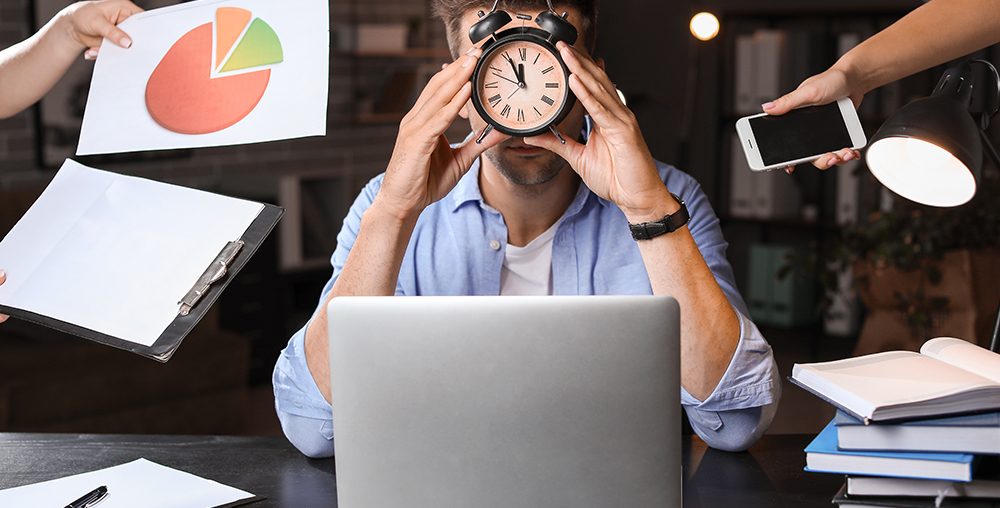
By: Scott Converse
One of the most asked questions I receive is, “how can I work more efficiently?” Individuals and groups that have been successful at making work more efficient tend to follow a similar approach. Let’s break down what they focus on in order to create workplace improvements.
Frequently, work done in a business setting is process related. A process has a beginning and an end, it creates an output or fulfills a request, and it repeats. A process might create a product, fulfill an order, or help a customer with a question or an ailment. We often create functional groups within our organizations to perform process activity. Unfortunately, the work performed by these functional groups can become frustrating, siloed, and not create the best outcomes for those who originally asked for the request to be fulfilled. When group work is based on process activity, look to these four root cause areas that might be creating some of the inefficiency or frustration in the system.
Understand the Whitespace
Most processes span more than one group. It’s important to understand the hand-offs that take place between upstream and downstream functional groups. Frequently the frustration felt by process workers and customers is rooted in the idle time handoffs between each step. I call this idle time frustration whitespace. It may take you only minutes or hours to perform your part of the process activity successfully, but the hand off or whitespace before the next group performs their work is days, weeks, or months. Reduce and eliminate whitespace whenever possible.
Reduce Rework
Another source of process inefficiency is the rework caused by mistakes, errors, or other activities that don’t help to create the fulfilled customer request. Unfortunately, many groups focus just on error identification. We want to also understand what causes the mistake and reduce or eliminate the mistakes in the future. Don’t try for perfection the first time you look at improving rework. It’s about making work better, not making work perfect. Reduce and eliminate rework whenever possible.
To Vary or Not to Vary
Processes repeat, it’s what makes a process a process. Sometimes it’s the goal of process-driven work to fulfill the same request again and again. If so, we want to understand the variation upstream that might make it more difficult to perform our process work. We also want to look at our output and determine if there’s any variation that was created that isn’t a necessary part of the request being fulfilled successfully. Understand and reduce the variation whenever possible.
That said, sometimes our requests vary because our customers demand variety, or the mission of the organization is to embrace diversity. In those situations, we need to focus on building and maintaining systems and processes that are robust enough to accept all the different types of requests we want to support and process those requests as efficiently as possible. Understand and embrace variation when it is necessary and valuable.
See It, Name It, Improve It
Inefficiency creeps into process work, in the same way that dust gathers in your home. No one wants to be frustrated or inefficient in their work activities; no one wants a dusty, dirty, cluttered home. In both examples it builds up over time. To help workplace inefficiencies that build up, have teams go to where the work is being performed and observe work activities. When the activity is frustrating, inefficient, or doesn’t really add value to the initial request, note it.
Ideally, have the group agree on seven or eight general category types for common workplace problems and then place those observed inefficiencies into the named category types. After the group observation is complete, begin the work of reducing or eliminating those workplace frustrations. Once you name it, then you can claim it as a problem and start improving it. Many of you recognize this approach as a core philosophy behind Lean Thinking and a quick internet search on Lean Wastes will give you many examples of what to call your different category types of inefficiency or waste.
It’s about improving the whole, not optimizing a single part of the system.
Scott Converse
Collaboration begins when groups realize that they are only a part of the whole interconnected process; it’s about improving the whole, not optimizing a single part of the system. Visual tools often help groups see the whole. Simple process maps or flow charts are very revealing. Making sure the whole group is focused on what is to be improved and what isn’t going to be improved is critical. The overused cliché, “make sure everyone in the canoe is paddling in the same direction,” comes to mind. Group problem solving tools like goal statements, group project charters, roles and responsibility matrices, and decision-making rules help everyone paddle in the same direction.
For more on process improvement, data driven problem solving, group dynamics, and making work better, we’ve developed a three-day program that explores two power methodologies and over two dozen specific problem-solving tools. You can learn more about Business Process Improvement Using Lean Six Sigma and Performance Metrics by visiting our website.
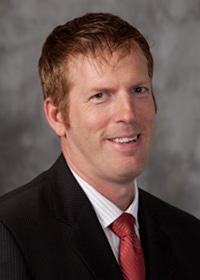
Scott Converse teaches Process Improvement and Project Management programs for the Wisconsin School of Business Center for Professional & Executive Development. To learn more about these programs, view our Lean Six Sigma and Project Management Certificates.